![]() |
![]() |
||||||||||||||||||||||||||||||||||||||||||||||||||||||||||||||||||||||
Химическое лужение
Автор: Sobiratel_sxem Добрый день, уважаемые радиолюбители. В предыдущих частях данной статьи мы рассмотрели как проводится предварительная подготовка поверхности стеклотекстолита перед изготовлением печатной платы, как наносится защитный рисунок, а так же рассмотрели множество рецептов травления проводящего рисунка. Сегодня мы продолжим рассматривать процесс изготовления печатных плат и рассмотрим процесс химического лужения [1-5]. Итак, после окончания процесса травления необходимо тщательно промыть заготовку с готовым проводящим рисунком большим количеством воды для удаления остатков травильного раствора. Далее следует удалить остатки фоторезиста с поверхности проводящего рисунка. Для этого необходимо приготовить 3% раствор гидроксида натрия (каустической соды, натриевой щёлочи, NaOH) либо гидроксида калия (едкого кали, калиевой щёлочи, KOH), опустить туда протравленную заготовку и покачивая ёмкость дождаться отслаивания фоторезиста от поверхности. Для ускорения процесса можно воспользоваться кистью с жёстким ворсом, либо промыть заготовку руками в латексных (нитриловых) перчатках [6]. На видео ниже данный процесс показан в реальном времени: На фото данный процесс выглядит вот так:
После удаления фоторезиста заготовку необходимо тщательно промыть в том же самом 3% растворе щёлочи, либо порошковым чистящим средством типа «Сорти» или «Пемолюкс» (или им подобным по составу). Далее заготовка тщательно промывается большим количеством воды для удаления остатков щёлочи (чистящего средства) и насухо протирается бумажной салфеткой либо ХБ тканью. Теперь осталось обезжирить поверхность ацетоном или изопропиловым спиртом (я рекомендую использовать ацетон) и можно переходить к процессу химического лужения. Внимание! После обезжиривания поверхности проводящего рисунка НЕ ПРИКАСАЙТЕСЬ голыми руками к поверхности т.к. на ней останутся потожировые следы и процесс обезжиривания придётся повторить заново! Для химического лужения необходимо в ёмкость подходящего размера и объёма налить раствор для химического лужения (продаваемый под наименованием «жидкое олово») так, что бы слой над погружённой заготовкой составлял не менее 1 сантиметра, погрузить подготовленную (и обезжиренную) заготовку в раствор и, время от времени (раз в 5-10 минут) покачивая ёмкость для перемешивания раствора, выдержать 20-30 минут. За это время поверхность медного проводящего рисунка равномерно покроется оловом (или сплавом олово-висмут, в зависимости от типа раствора) [7]. После этого заготовку можно извлечь из раствора, промыть водой, ополоснуть 3% раствором щёлочи (либо порошковым чистящим средством — без фанатизма) и тщательно смыть большим количеством воды остатки щёлочи (чистящего средства). После этого заготовку необходимо вытереть бумажной салфеткой либо ХБ тканью. На этом процесс химического лужения можно считать оконченным. В подборке фото ниже показан пример плат, покрытых заводским составом для химического лужения. Если перед нанесением защитного рисунка подготовленная поверхность у Вас была матовой, то и покрытая химически поверхность так же будет матовой, а если была глянцевой — покрытая поверхность также будет глянцевой. Это связано с тем, что подобные покрытия обладают небольшой толщиной и предназначены, прежде всего, для улучшения паяемости печатных плат. Покрытия такой толщины физически не способны изменить ощутимо исходную морфологию поверхности. Если же на будущей печатной плате необходимы отверстия под выводные компоненты, то сверловку отверстий лучше произвести до химического лужения, а после сверловки заготовку тщательно промыть водой, ополоснуть щёлочью (или порошковым чистящим средством), обезжирить и провести процесс лужения. На этом процесс изготовления печатной платы в домашних условиях можно считать оконченным.
Дополнительно следует отметить, что хорошая паяемость печатных плат с химически полученным финишным покрытием (лужением) гарантированно сохраняется в течении 1-6 месяцев в зависимости от условий хранения. Кроме того, на смонтированные печатные платы необходимо дополнительно наносить защитное покрытие (лак или компаунд) т.к. во время хранения и эксплуатации (особенно во влажной среде) со временем олово будет окисляться. В результате печатные узлы, как минимум, примут непрезентабельный вид. В подборке фото ниже представлена пара опытных образцов печатных узлов при проведении испытаний.
А на этом на сегодня все… Ага, мечтать не вредно. Поверили что статья по химическому лужению будет столь короткой? Зряяяя, потому как самое интересное впереди! Заводской состав для химического лужения — это хорошо, но на мой взгляд его стоимость слишком сильно завышена. Да и в продаже достаточно часто попадаются не совсем свежие растворы, эффективность которых ощутимо ниже. В связи с этим неплохо бы научиться изготавливать подобные составы дома по мере необходимости. Именно этому и будет посвящён остаток данной части статьи. Иммерсионные процессы (химическое лужение) — это контактное восстановление металлов из их растворов на электроотрицательных поверхностях. При таком восстановлении происходит реакция замещения металла основы (в данном случае меди) на металл из раствора (олово, сплав олово-висмут, серебро, золото и пр.). Если на осаждаемой поверхности образуется плотная металлическая пленка, ее можно использовать в качестве функционального покрытия — чаще всего в качестве покрытия печатных плат под пайку (т.е. в качестве финишного покрытия). Так, например, для иммерсионного оловянирования достаточно просто опустить заготовку в водный раствор, содержащий хорошо растворимую соль олова (обычно — хлористое олово). Выделение олова на поверхности меди происходит при погружении в такой раствор соли олова, в котором потенциал меди более электроотрицателен, чем материал покрытия. Изменению потенциала в нужном направлении способствует введение в раствор соли олова комплексообразующей добавки — тиомочевины либо цианида щелочного металла. Таким образом наиболее распространёнными составами для химического оловянирования являются составы, представленные на фото ниже [8, 9].
Рассмотрев представленные составы можно отметить, что состав под номером 3 не подходит для домашнего использования т.к. содержит достаточно токсичный цианистый калий (LD50 около 1.7 мг/кг). Механизм смещения потенциала в растворе под номером 4 не совсем ясен — не удивительно, что не удалось подобрать условия, в которых данный раствор бы работал должным образом. Раствор под номером 5 я не испытывал на практике из-за отсутствия квасцов на момент покупки необходимых реактивов (если кто-то пробовал на практике данный состав — отпишитесь, пожалуйста, о полученном результате). Таким образом в качестве основных экспериментальных растворов использовались несколько модернизированные растворы под номерами 1 и 2. Итоговые растворы имели следующий состав:
Раствор №1:
Раствор готовится следующим образом: в 0.5 литрах дистиллированной воды растворяется 150 г. молочнокислого натрия; после полного растворения раствор нагревается на водяной бане до температуры 50-60 градусов Цельсия; присыпается 70 г. тиомочевины и перемешивается до полного растворения; далее приливается 120 мл. 30% раствора серной кислоты и снова перемешивается; добавляется 20 г. двухлористого олова и перемешивается до полного растворения; дистиллированная вода доливается до получения объёма 1 литр; раствор тщательно перемешивается и оставляется остывать до комнатной температуры. После полного остывания раствор переливается в герметичную тару и хранится без доступа воздуха и прямых солнечных лучей. Готовый раствор прозрачный, имеет соломенно-жёлтый цвет и небольшой запах молочной кислоты. Хранится в целом неплохо. Через месяц хранения на дне выпадает небольшое количество чёрного осадка общим объемом в 3-5 спичечных головок — т.е. раствор достаточно стабилен.
Раствор №2:
Данный раствор готовится так же и в том же порядке что и предыдущий, но вместо натрия молочнокислого используется гидроксид натрия. Готовый раствор практически прозрачен (с небольшим желтоватым оттенком). Хранится значительно хуже. Через месяц хранения на дне выпадает твёрдый нерастворимый желтоватый осадок размером 2х1.5х1 см. Аналогичный по консистенции осадок выпадает и в заводских растворах для химического лужения.
Раствор №3:
Раствор готовится следующим образом: в 0.5 литрах дистиллированной воды растворяется 40 г. винной кислоты; после полного растворения раствор нагревается на водяной бане до температуры 50-60 градусов Цельсия; присыпается 50 г. тиомочевины и перемешивается до полного растворения; далее добавляется 20 г. двухлористого олова и перемешивается до полного растворения; дистиллированная вода доливается до получения объёма 1 литр; раствор тщательно перемешивается и оставляется остывать до комнатной температуры. После полного остывания раствор переливается в герметичную тару и хранится без доступа воздуха и прямых солнечных лучей. Готовый раствор прозрачен, оттенка не имеет. Хранится в целом неплохо. Через месяц хранения на дне выпадают красивые кристаллы хлорида олова (см. подборку фото ниже), растворяющиеся при нагревании раствора на водяной бане.
Раствор №4:
Способ и порядок приготовления данного раствора аналогичен раствору №1, но вместо серной кислоты используется винная кислота, а вместо натрия молочнокислого — гипофосфит натрия в указанных концентрациях. Готовый раствор прозрачен, оттенка не имеет. Хранится в целом неплохо. Через месяц хранения на дне выпадает тонкий слой чёрного осадка (раза в 2-3 больше, чем в растворе №1). — т.е. раствор достаточно стабилен [8, 9].
Раствор №5: Заводской состав для химического лужения Жидкое олово[7]. После приготовления описанных выше растворов, а так же выдержки в закрытой таре в течение одного месяца (в целях наблюдения за стабильностью растворов) был проведён ряд сравнительных экспериментов. Для проведения экспериментов было подготовлено 5 заготовок, разделённых на 6 одинаковых независимых зон (см. подборку фото ниже). Каждая заготовка была покрыта одним из составов химического лужения, описанных выше. Температура растворов — комнатная. В каждом растворе заготовка выдерживалась 30 минут с перемешиванием раствора каждые 10 минут. После этого заготовка ополаскивалась водой, промывалась 3% раствором щёлочи, снова тщательно промывалась водой для отмывки остатков щелочи. В самом конце заготовка насухо вытиралась бумажной салфеткой.
В подборке видео ниже показан процесс химического лужения заготовки в реальном времени в момент опускания в раствор: на левом видео — раствор с составом №2, на правом видео — в раствор с составом №4. После подготовки необходимого количества заготовок на каждую заготовку по зонам был нанесён различный флюс либо паяльная паста. Это выполнялось в следующем порядке (считая сверху вниз): первая зона — концентрированный раствор канифоли в изопропиловом спирте; вторая зона — чистый глицерин; третья зона — активный флюс Multicore Hydro-Х/20, четвёртая зона — паяльная паста Multicore (Henkel) WS200; пятая и шестая зоны — не наносилось ничего [10-15]. После этого все заготовки были пропущены через конвекционную печь с типовым температурным профилем для оплавления паяльных паст. Далее заготовки были тщательно отмыты изопропиловым спиртом, а так же водой, хорошо просушены струёй теплого воздуха. Данные процессы, а так же параметры термопрофиля показаны в подборке фото ниже. Заготовки на фото расположены согласно номерам растворов для химического лужения, считая справа налево.
С первого взгляда может показаться, что на фото творится какой-то ужас, но попробуем разобраться что же произошло и чем нам это может помочь. Изначально следует отметить, что результат со всеми растворами химического лужения получился практически идентичным т.е. характеристики покрытий, получаемых в разных рецептурах практически идентичны друг другу (что не удивительно, учитывая механизм получения подобных покрытий). 1. Итак, по первой зоне отлично видно, что при нагревании выше 200 градусов Цельсия канифоль способна не только удалять окислы со спаиваемых поверхностей и обеспечивать необходимую смачиваемость, но и корродировать осаженное химически олово. Основной состав канифоли — смоляные кислоты (80-90% из которых составляет абиетиновая кислота). Наиболее сильное корродированние отмечается на заготовке, покрытой составом №5 т.е. заводским жидким оловом [16-18]. Такое поведение может стать проблемой при пайке компонентов на печатную плату с использованием жидкой спиртоканифоли (и подобных ей флюсов) и паяльного фена. В этом случае канифоль будет растекаться и возможно образование подобных участков вокруг паяного соединения. На функциональность это не повлияет, но внешний вид изделия будет испорчен. При использовании же твёрдой канифоли и паяльника (паяльной станции) подобной проблемы особо не возникает (см. представленные выше фото со смонтированными опытными образцами) т.к. время нагрева зоны пайки, а соответственно и время повышенной активности флюса значительно ниже. Кроме того в очередной раз подтверждается давно известный факт — всегда необходимо отмывать с поверхности печатных плат любые остатки флюса для устройств, работающих при повышенных температурах и влажности (несмотря на то, что при комнатной температуре и относительно небольшой влажности канифоль считается защитным покрытием). А при необходимости нанесения защитных лаков и компаундов производить тщательную отмывку придется в любом случае [19]. 2. Во второй зоне экспериментальных заготовок был нанесён глицерин. Глицерин по химической природе — спирт, бесцветная вязкая жидкость. Не имеет запаха, на вкус сладкая (за что глицерин и получил своё название). Отличительной чертой глицерина является его высокая гигроскопичность т.е. способность поглощать воду из атмосферы (до 40% по массе). Несмотря на то, что глицерин использовался в максимально доступной концентрации (99.5%), всё же небольшое количество воды в нём присутствовало. Именно этим можно объяснить локальное окисление покрытий в местах скопления капель глицерина. Ни на одной из заготовок покрытие не было как-то ощутимо повреждено [13-15]. Подобная низкая химическая активность по отношению к покрытию была бы неплохим основанием для использования глицерина в качестве основы для флюсов (что часто и делается), если бы не одно НО — он гигроскопичен. Суть в том, что материал печатных плат представляет из себя достаточно пористый материал, «неплохо» впитывающий и удерживающий в порах остатки используемых флюсов. При этом мне, например, неизвестны даже промышленные способы надёжной отмывки остатков глицериновых флюсов с печатных плат (особенно из под микросхем и надёжного вымывания из пор поверхностных слоёв печатных плат). Если обобщить 2 этих факта, то получается не особо хорошая картина — не до конца отмытые остатки глицерина со временем будут напитывать из воздуха влагу, что явно ни к чему хорошему не приведёт ни в сигнальных цепях с высоким сопротивлением, ни с точки зрения коррозии. Возможно проблему можно было бы решить отмывкой печатных узлов в 2 этапа. На первом этапе использовать ультразвуковую отмывку в хорошо текучем растворителе, способном растворять глицерин (например, ацетоне), а на втором этапе использовать 2-3 ступени струйной отмывки с последующей сушкой горячим воздухом. Но, как вы понимаете, для радиолюбителей такой способ практически не пригоден и не применим. Да и вопросы относительно устойчивости некоторых пластиковых корпусов к действию растворителя остаются открытыми. В связи с этим я бы не рекомендовал использовать глицерин и флюсы на основе глицерина для ручной пайки печатных узлов в домашних условиях (несмотря на то, что они очень популярны). 3. В третьей зоне был нанесён активный флюс Multicore Hydro-Х/20. Само собой, благодаря своей активности данный флюс достаточно сильно корродировал оловянное покрытие. Однако, подобного эффекта в реальности стоит опасаться при использовании подобных активных флюсов при пайке радиокомпонентов на печатные платы с использованием паяльного фена. Аналогично зоне со спиртоканифолью флюс может растекаться по плате и образовывать подобные участки вокруг паяных соединений. На функционирование устройства это особо не повлияет, но внешний вид изделия будет испорчен. Кроме того, при ручной пайке с использованием данного флюса такой проблемы не возникает (см. фото смонтированных опытных образцов в подборке выше). Тут не стоит забывать о том, что любые активные флюсы требуют обязательной полноценной отмывки после окончания монтажа. Для описанных в статье покрытий отмывку необходимо произвести в течении суток после начала монтажа печатного узла. В противном случае на поверхности покрытия возможно появление темных участков окисляющегося олова. Отмывка проводится в 2 этапа. На первом этапе следует тщательно промыть печатный узел в слабом щелочном растворе (например, 3% растворе гидроксида натрия, гидроксида калия, кальцинированной соды либо чистящего средства типа Сорти или Пемолюкс. Идеальной будет промывка с использованием ультразвуковой ванны). На втором этапе следует тщательно промыть плату чистой водой для удаления остатков щелочей и загрязнений. После этого рекомендуется высушить плату потоком тёплого воздуха (например, феном). Данным флюсом для выводного монтажа (монтажа в отверстие), а так же монтажа SMD компонентов на печатные платы мы пользуемся на производстве более 10 лет и при должном применении он даёт отличный результат (вплоть до возможности залуживания окислившейся меди — см.подборку фото ниже) [11]. 4. В четвёртой зоне была нанесена паяльная паста Multicore (Henkel) WS200. Данная паста изготавливается на основе припоя, содержащего свинец. После пайки остатки флюса требуют обязательной отмывки (т.е. флюс является активным). По четвертой зоне хорошо видно, что паяльная паста оплавилась в целом неплохо. В связи с этим возможно использование описанных выше покрытий для пайки с использованием паяльных паст. Но при этом нужно правильно нанести паяльную пасту на контактные площадки — вся площадь площадки должна быть покрыта слоем паяльной пасты т.е. наносить пасту лучше всего через специализированный трафарет (методом трафаретной печати). Кстати говоря, растворение подобных финишных покрытий при пайке в общем объёме припоя паяного соединения является нормальным явлением (несмотря на то, что в некоторых случаях может создавать определённые проблемы в виде повышенного количества интерметаллидов) [12]. 5. В пятой и шестой зоне не наносилось никаких паяльных паст и флюсов — они были оставлены для экспериментов по ручной пайке и лужению. По представленным выше фото хорошо видно, что покрытие при прохождении через печь практически не пострадало — немного окислилось в местах попадания флюса из зоны с паяльной пастой и загрязнилось испаряющимися остатками флюса. Несмотря на это по данному покрытию лужение дорожек с использованием флюса Multicore Hydro-Х/20 и припоя ПОС-61 не представляет сложности и производится без каких-либо проблем. Так же хорошо удаётся выполнить и монтаж радиокомпонентов (см. подборку фото ниже, а так же фото смонтированных опытных образцов выше). Следует заметить, что на представленных образцах показан сам факт поведения покрытий при тех или иных воздействиях, возможности лужения и пайки данных покрытий, а так же исходный внешний вид. Я не стремился к какой-то эстетике и красивому итоговому внешнему виду. Само собой все описанные процедуры можно выполнить значительно качественнее (например, это хорошо видно по смонтированным опытным образцам).
Подводя итог можно сделать вывод о том, что использование для химического лужения описанных составов позволяет получить достаточно неплохо паяемые покрытия и хороший внешний вид конечных печатных узлов (несмотря на имеющиеся мелкие недостатки вроде необходимости покрытия законченных узлов защитным лаком или компаундом). Само собой, Вы всегда можете использовать для своих печатных плат классические методы лужения, но они займут у Вас на больших платах (особенно при использовании мелких компонентов) значительно больше времени по сравнению с химическим лужением. Кроме того, может возникнуть некоторые проблемы с дальнейшей установкой и пайкой микросхем с небольшим шагом выводов (т.к. будет необходимо обеспечить лужение без наплывов припоя). Улучшить паяемость и срок хранения описанных составов можно добавлением 5-7 г/л нитрата висмута. Подобная добавка позволяет осаживать из раствора сплав олово-висмут с содержанием висмута до 1.5-2% [8, 9]. Если при нанесении покрытий итоговые покрытия получаются рыхлыми (стираются ватным тампоном или ХБ тканью при протирке без фанатизма) либо появляются белёсые матовые пятна (похожие на размазанный пластилин), то в 80% случаев поверхность перед осаждением покрытия была подготовлена некачественно. В остальных 20% случаев виноват сам раствор для осаждения покрытия (раствор слишком загрязнён либо истощился). В таких ситуация в итоге платы будут выглядеть так, как это показано в подборке фото ниже. Выход из данной ситуации всего 1 — удалить механически (мелкой наждачной бумагой) получившейся слой, повторно подготовить поверхность и провести повторное осаждение в свежем растворе.
Ну и в качестве небольшого отступления на закуску — в домашних условиях возможно получение не только оловянного покрытия и сплава олово-висмут, но и, например, олово-свинец и некоторых других. Осаждение отдельных покрытий при этом связано с достаточно высокой токсичностью используемых компонентов электролита (например, цианистого калия) и не может рекомендоваться для использования в домашних условиях [8, 9, 20]. А на этом на сегодня всё, с уважением, Андрей!
P.S. Кстати, учитывая тот факт, что изготовление 5 одинаковых опытных образцов заняло ощутимое время, половину из которого приходится банально ждать завершения того или иного технологического процесса, было необходимо его чем-то занять. В свободные промежутки времени я решил пронаблюдать за хемилюминесценцией люминола. В качестве доступного источника люминола мной было использовано лекарственное средство Галавит (основное действующее вещество натриевая соль Люминола). Как изготовить исходные растворы для проведения реакции можно посмотреть тут или вот тут. Хемилюминесценция на фото выглядит достаточно красиво:
А на видео выглядит вот так:
Список использованной литературы:
Все вопросы в Форум.
|
|
||||||||||||||||||||||||||||||||||||||||||||||||||||||||||||||||||||||
![]() |
![]() |

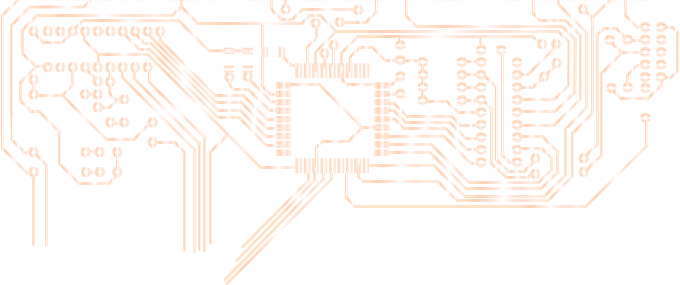
![]() |
![]() |
|||
|
||||
![]() |
![]() |